Advanced plastic extrusion solutions for manufacturers
Advanced plastic extrusion solutions for manufacturers
Blog Article
A Comprehensive Overview to the Refine and Benefits of Plastic Extrusion
In the large world of manufacturing, plastic extrusion emerges as a extremely effective and crucial procedure. Transmuting raw plastic right into continual profiles, it caters to a plethora of industries with its amazing adaptability.
Comprehending the Basics of Plastic Extrusion
While it might appear facility in the beginning glimpse, the procedure of plastic extrusion is basically straightforward - plastic extrusion. It is a high-volume manufacturing method in which raw plastic is thawed and formed right into a continuous profile. The procedure starts with the feeding of plastic product, in the type of granules, powders, or pellets, right into a warmed barrel. The plastic is then melted making use of a mix of warm and shear, applied by a revolving screw. As soon as the molten plastic reaches completion of the barrel, it is required via a tiny opening known as a die, forming it right into a desired type. The shaped plastic is after that cooled down, strengthened, and reduced right into preferred sizes, completing the process.
The Technical Process of Plastic Extrusion Explained

Sorts Of Plastic Suitable for Extrusion
The selection of the right type of plastic is an essential aspect of the extrusion procedure. Different plastics supply distinct buildings, making them much more suited to particular applications. Polyethylene, as an example, is commonly used as a result of its inexpensive and easy formability. It offers outstanding resistance to chemicals and moisture, making it ideal for items like tubing and containers. Similarly, polypropylene is an additional prominent selection due to its go to these guys high melting factor and resistance to tiredness. For more durable applications, polystyrene and PVC (polyvinyl chloride) are often selected for their toughness and durability. Although these are common Homepage options, the selection inevitably relies on the particular demands of the item being produced. Comprehending these plastic types can dramatically boost the extrusion procedure.
Contrasting Plastic Extrusion to Various Other Plastic Forming Approaches
Understanding the kinds of plastic appropriate for extrusion leads the method for a broader conversation on exactly how plastic extrusion piles up versus various other plastic developing approaches. Plastic extrusion is unrivaled when it comes to creating continuous profiles, such as seals, pipes, and gaskets. It also permits for a consistent cross-section along the size of the item.
Key Advantages of Plastic Extrusion in Manufacturing
In the world of production, plastic extrusion supplies many substantial advantages. One remarkable advantage is the cost-effectiveness of the process, which makes it a financially enticing manufacturing method. In addition, this method supplies remarkable item flexibility and enhanced manufacturing speed, thus boosting general manufacturing performance.
Economical Manufacturing Technique
Plastic extrusion leaps to the leading edge as a cost-effective production technique in production. Furthermore, plastic extrusion needs less power than traditional production methods, adding to lower operational costs. Overall, the monetary advantages make plastic extrusion an extremely appealing choice in the manufacturing sector.
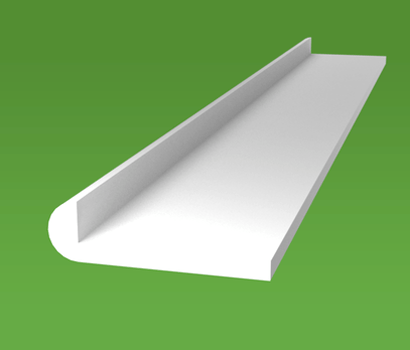
Superior Product Versatility
Beyond the cost-effectiveness of plastic extrusion, an additional substantial benefit in making lies in its premium product flexibility. This makes plastic extrusion an ideal remedy for sectors that need tailored plastic parts, such as automotive, building, and packaging. In essence, plastic extrusion's item flexibility cultivates advancement while boosting functional efficiency.
Enhanced Production Speed
A substantial advantage of plastic extrusion exists in its boosted manufacturing rate. Few other production processes can match the speed of plastic extrusion. Furthermore, the capacity to keep regular high-speed production without giving up product high quality establishes plastic extrusion apart from other approaches.
Real-world Applications and Impacts of Plastic Extrusion
In the world of manufacturing, the method of plastic extrusion holds profound importance. The economic advantage of plastic extrusion, Your Domain Name mostly its high-volume and cost-efficient result, has transformed manufacturing. The sector is constantly aiming for technologies in recyclable and eco-friendly materials, indicating a future where the benefits of plastic extrusion can be maintained without endangering environmental sustainability.
Final thought
Finally, plastic extrusion is a effective and extremely reliable approach of transforming basic materials right into diverse items. It offers countless benefits over other plastic forming approaches, including cost-effectiveness, high result, very little waste, and layout flexibility. Its impact is profoundly really felt in various industries such as building and construction, auto, and customer goods, making it a pivotal process in today's manufacturing landscape.
Diving much deeper into the technical process of plastic extrusion, it begins with the option of the ideal plastic product. When cooled down, the plastic is cut right into the required sizes or wound onto reels if the item is a plastic movie or sheet - plastic extrusion. Contrasting Plastic Extrusion to Various Other Plastic Forming Techniques
Understanding the types of plastic appropriate for extrusion paves the method for a broader conversation on how plastic extrusion piles up versus various other plastic creating techniques. Few other manufacturing processes can match the rate of plastic extrusion.
Report this page